At Chempharm India, we provide advanced HVAC systems designed to maintain critical temperature, humidity, and air quality in controlled environments. Our solutions cater to industries including pharmaceuticals, food and beverages, and electronics, where precise environmental control is essential. We focus on energy-efficient designs, seamless integration, and compliance with industry standards, ensuring optimal performance and safety for cleanrooms and sensitive operational spaces.
What is HVAC?
HVAC usually refers to the mechanical system that provides heating, ventilation and/or cooling within a residential or commercial building or a premise. An HVAC system is designed to control the environment in which it functions. HVAC system does this by controlling the air cleanliness of the air in that environment.
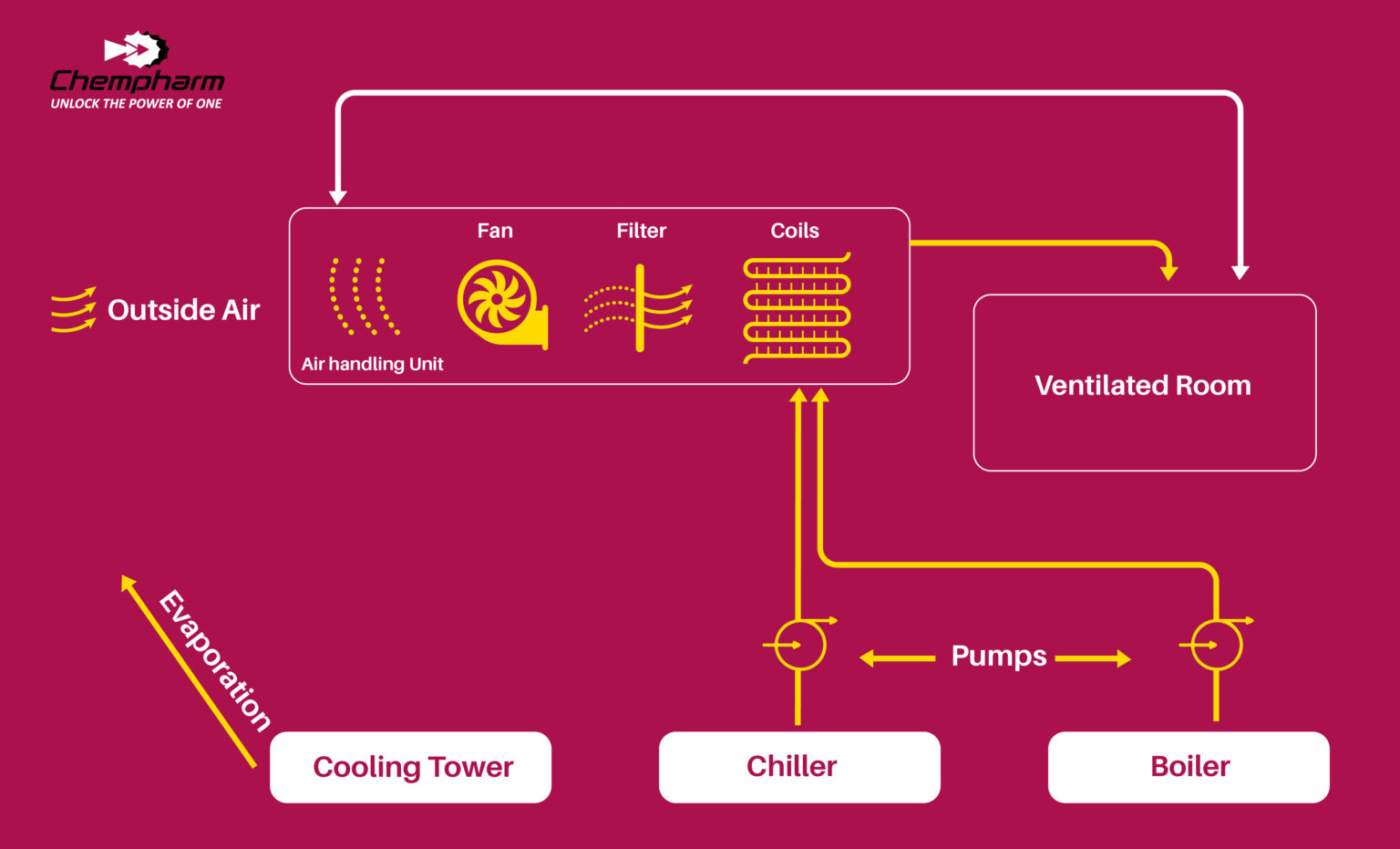
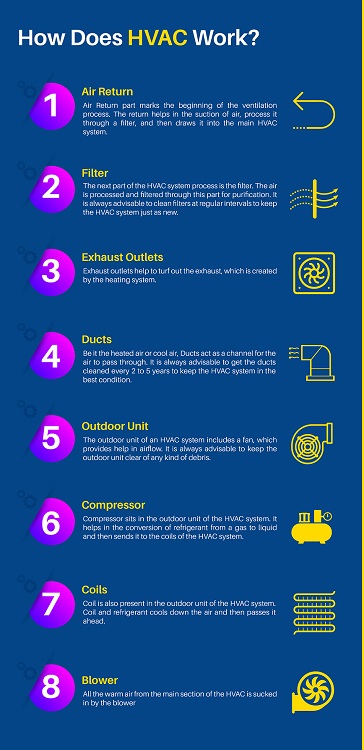
Types of HVAC Systems?
The most common types of HVAC systems are as follows:
Heat Pump – Heat pumps sucks in heat from a cold space or environment and warms it to release in the room to maintain the temperature
Rooftop Unit – Rooftop HVAC systems are usually preferred to manage the temperature of a large space. It is a large unit which is placed on the rooftop of the building
Water Source Heat Pump – This type of HVAC system is uncommon in today’s time as geothermal HVAC systems are picking up the trend nowadays. The water source heat pump is exactly what the name suggests as they require proximity to a body of water to work
Packaged HVAC – Packaged HVAC systems are similar to the rooftop HVAC systems but are preferred for smaller areas/rooms or domestic use.
Split System HVAC – Split system HVAC means that there are 2 units of the system – outdoor and indoor. There are two types of split system HVAC – ductless and central)
Ductless HVAC – These HVAC systems are the most preferred HVAC systems for a single large room or multiple small rooms.
Which is the Best HVAC System available?
Chempharm India provides the best HVAC system available in the market. You can ASK CHEMPHARM EXPERTS to design a most customized HVAC system as per your requirement and budget. To ensure best quality, Chempharm India incorporates the following key elements: (HVAC SYSTEM FOR CLEAN ROOM)
Clean Room HVAC System – The integrity of the cleanroom environment is created by the pressure differential compared with adjacent areas through air flow pattern.
The HVAC system requirements include:
Supplying airflow in sufficient volume and cleanliness to support the cleanliness rating of the room
Introducing air in a manner to prevent stagnant areas where particles could accumulate
Filtering the outside and re-circulated air across high efficiency particulate air (HEPA) filters
Conditioning the air to meet the cleanroom temperature and humidity requirements
Ensuring enough conditioned makeup air to maintain the specified positive pressurization
Monitoring systems – Monitoring systems include a means of indicating that the cleanroom is functioning properly. The variables monitored are the pressure differential between the outside environment and the cleanroom, temperature, humidity and, in some cases, noise and vibrations. Control data should be recorded on a routine basis.
HVAC System Design for Clean Facility– HVAC systems in cleanrooms are substantially different from their counterparts in commercial buildings in terms of equipment design, system requirements, reliability, size and scale.
Cleanroom HVAC Vs Air Conditioned Space
Increased Air Supply: Whereas comfort air conditioning would require about 2-10 air changes/hr, a typical cleanroom would typically require 30 – 80 air changes and could be as high as 600 for absolute cleanliness.
The use of high efficiency filters: The use of high efficiency particulate air (HEPA) filters having filtration efficiency of 99.9997% down to 0.3 microns is another distinguishing feature of cleanrooms. The HEPA filters for stringent cleanrooms are normally located at the terminal end and in most cases provide 100% ceiling coverage.
De-humidifiers in few cases would be needed to control RH in the HVAC systems for hygroscopic pharma products or specialized electronic sectors .
Room pressurization: The cleanroom is positively pressurized (to 0.05 in-wc) with respect to the adjacent areas. This is done by supplying more air and extracting less air from the room than is supplied to it.